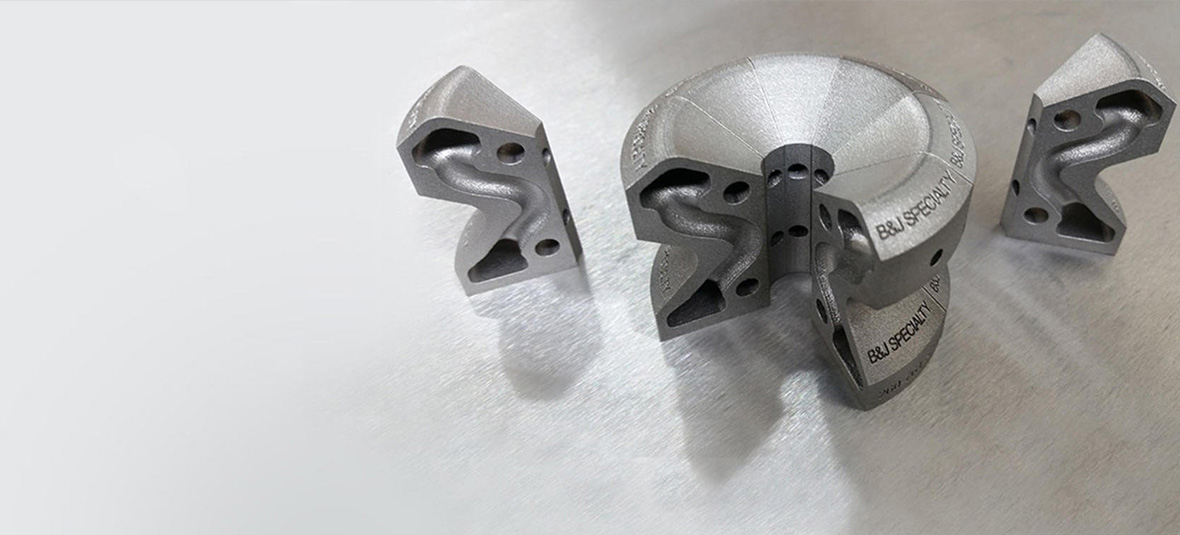
B&J Specialty 通过金属 3D 打印随形冷却注塑模具将生产率提高 30%
CHALLENGE 挑战
Increase productivity of injection molding for an automotive duct that required a long tooling cycle to avoid warpage.
提高汽车管道的注塑成型生产率,该管道需要较长的模具周期以避免翘曲。
SOLUTION 方案
- Cimatron® integrated CAD/CAM software
Cimatron® 集成 CAD/CAM 软件
RESULTS 结果
- Accelerated cycle cooling time from one minute to 40 seconds.
将循环冷却时间从 1 分钟缩短到 40 秒。 - Increased duct production rate by 30%.
风管生产率提高 30%。 - Reduced temperature variation across cooling by 86%.
冷却过程中的温度变化减少了 86%。 - Extended mold lifetime from reduced molding pressure.
通过降低成型压力延长模具寿命。 - Produced parts that consistently meet tough quality requirements.
生产的零件始终满足严格的质量要求。 - Delivered higher-quality parts with more efficient cooling, which enabled time and cost savings for tool builders and mold operators.
提供具有更高效冷却的更高质量的零件,从而为工具制造商和模具操作员节省时间和成本。
Large temperature variations in an injection-molding cooling cycle can dramatically increase the risk of parts warping. When tests of a conventionally-designed and manufactured injection-molded automotive duct yielded temperature fluctuations of 132˚C throughout the process, B&J Specialty, Inc. recommended conformally-cooled mold inserts to its client for more even cooling.
注塑成型冷却循环中的大温度变化会大大增加零件翘曲的风险。当对传统设计和制造的注塑成型汽车管道进行测试时,在整个过程中产生了132°C的温度波动,B&J Specialty, Inc.向其客户推荐了随形冷却的模具嵌件,以实现更均匀的冷却。
To achieve this, B&J Specialty engineers relied on Cimatron CAD/CAM software to design the molds and conform the internal cooling channels parallel to the part’s surface. To deliver these complex internal conformal cooling channels accurately, they used metal additive manufacturing (AM) on a ProX DMP 300 printer for production.
为了实现这一目标,B&J Specialty 工程师依靠 Cimatron CAD/CAM 软件来设计模具,并使内部冷却通道平行于零件表面。为了准确地提供这些复杂的内部随形冷却通道,他们在 ProX DMP 300 打印机上使用金属增材制造 (AM) 进行生产。
The new conformally-cooled mold insert reduced temperature variation throughout cooling to 18˚C and shrank cycle time on the mold from one minute to 40 seconds, an overall productivity improvement of 30 percent.
新型随形冷却模具嵌件将整个冷却过程中的温度变化减少到 18°C,并将模具的循环时间从 1 分钟缩短到 40 秒,整体生产率提高了 30%。
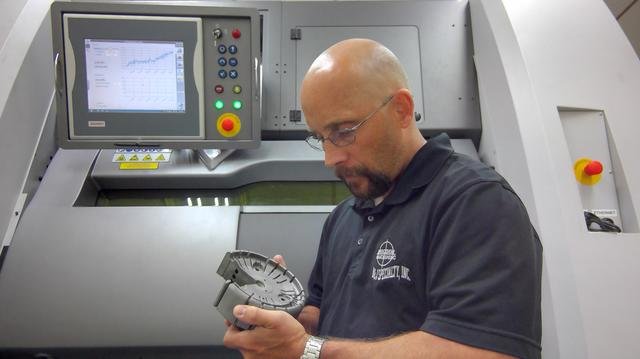
据 Jarod Rauch 称,ProX DMP 300 可以保持千分之三或千分之四英寸的公差。
Sub-Optimal Cooling Lines Lead to High-Temperature Variations
次优冷却管路导致高温变化
Conformally-cooled molds take advantage of modern technology to solve an age-old problem. Many injection-molded parts have curved surfaces, yet the drills used to create cooling channels only produce straight lines. In most cases, this means it is impossible to match cooling lines to part geometry. Conventionally-produced straight cooling lines have to run beyond the outermost features of the part to avoid interfering with the cavity, which means that features closer to the part’s center are typically far from the nearest cooling line. This often results in significant temperature variations over the volume of the part at the start of the cooling process.
随形冷却模具利用现代技术来解决一个古老的问题。许多注塑成型零件具有曲面,但用于创建冷却通道的钻头只能产生直线。在大多数情况下,这意味着无法将冷却管路与零件几何形状相匹配。传统生产的直线冷却管线必须超出零件的最外层特征,以避免干扰型腔,这意味着靠近零件中心的特征通常远离最近的冷却管线。这通常会导致在冷却过程开始时零件体积的温度发生显着变化。
The automotive duct that B&J Specialty redesigned for more-efficient cooling features multiple irregular and curved surfaces. In the original mold design, B&J drilled straight cooling lines through a hub and stator block that were used to adjust the mold geometry to account for warpage. As is often the case with irregular shapes, several key features of the duct were distanced from the cooling lines due to the limitation of the straight channels. The resulting temperature variations generated various residual stresses that tended to bend the part as it cooled. In the past, this problem was addressed by extending the cooling cycle to ensure the part was fully solidified before removing it from the mold and adjusting the inserts to account for any remaining warpage. The problem with this approach was that lengthening the cooling cycle reduced productivity and increased the cost of making the part.
B&J Specialty 为提高冷却效率而重新设计的汽车管道具有多个不规则和曲面。在最初的模具设计中,B&J 在轮毂和定子块上钻出直线冷却管路,用于调整模具几何形状以解决翘曲问题。与不规则形状的情况一样,由于直通道的限制,管道的几个关键特征与冷却管路保持距离。由此产生的温度变化会产生各种残余应力,这些残余应力往往会使零件在冷却时弯曲。过去,这个问题是通过延长冷却周期来解决的,以确保零件在从模具中取出之前完全凝固,并调整嵌件以解决任何剩余的翘曲。这种方法的问题在于,延长冷却周期会降低生产率并增加制造零件的成本。
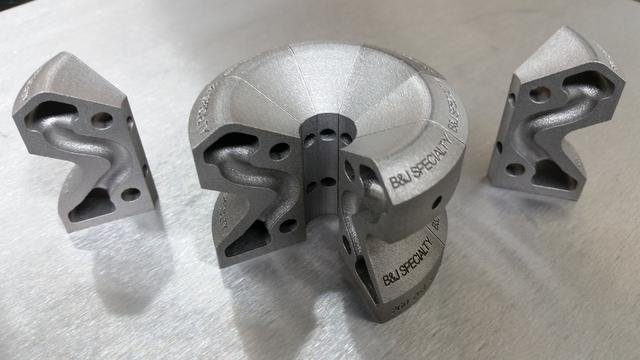
与传统的直线通道相比,金属 3D 打印随形冷却管线将温度变化减少了 86%。
Updating the Mold with Conformal Cooling Channels
使用随形冷却通道更新模具
According to B&J Specialty information technology and 3D printing manager Jarod Rauch, the automotive duct appeared to be a strong candidate for a modified conformal cooling design, which would help to improve final part quality, reduce scrap, and shrink the cooling cycle. B&J Specialty proposed this solution to their client, an automotive supplier, who agreed to test the new methodology. Provided with the CAD file of the original geometry, B&J engineers got to work using Cimatron mold design software. “Cimatron is pretty much a one-stop-shop software that allows us to have full CAD functionality for designing and gives us the option to roll right to build preparation from the same package.”
根据B&J Specialty信息技术和3D打印经理Jarod Rauch的说法,汽车管道似乎是改进的随形冷却设计的有力候选者,这将有助于提高最终零件质量,减少废品,并缩短冷却周期。B&J Specialty 向他们的客户(一家汽车供应商)提出了这个解决方案,后者同意测试新方法。有了原始几何形状的CAD文件,B&J工程师开始使用Cimatron模具设计软件工作。“Cimatron 几乎是一个一站式软件,它使我们能够拥有完整的 CAD 设计功能,并让我们可以选择从同一个软件包中直接构建准备工作。”
Rauch says B&J Specialty discovered Cimatron while researching metal 3D printers for conformal cooling applications. “We saw that Cimatron provides a complete end-to-end solution including mold design software, build preparation software, and 3D printers, which got me excited about this solution,” says Rauch. “Cimatron not only focuses on the machine, but it also focuses on how engineers design for additive.”
Rauch说,B&J Specialty在研究用于随形冷却应用的金属3D打印机时发现了Cimatron。“我们看到 Cimatron 提供了一个完整的端到端解决方案,包括模具设计软件、构建准备软件和 3D 打印机,这让我对这个解决方案感到兴奋,”Rauch 说。“Cimatron 不仅关注机器,还关注工程师如何设计增材制造。”
Working within Cimatron, B&J engineers removed the original straight cooling lines and replaced them with conformal ones that maintained a consistent distance from the part’s surface. Final mold production with metal 3D printing allowed the engineers to design complex channels with improved cross-sections and interface surfaces. These features help ensure turbulent flow, which further increases the amount of heat transferred from the mold to the coolant to assist with efficient cooling. The ability to cool molded parts more efficiently also helps ensure part quality by reducing the occurrence of part defects such as warping and sink marks. A direct path to higher-quality parts saves time and money for both the tool builder and the mold operator by limiting the number of corrections, trials, and sampling required to achieve the desired results.
在Cimatron内部,B&J工程师拆除了原来的直线冷却管路,取而代之的是与零件表面保持一致距离的保形冷却管路。使用金属 3D 打印进行最终模具生产使工程师能够设计出具有改进横截面和界面表面的复杂通道。这些功能有助于确保湍流,从而进一步增加从模具传递到冷却液的热量,以帮助高效冷却。能够更有效地冷却成型零件,还可以减少零件缺陷(如翘曲和凹痕)的发生,从而有助于确保零件质量。通过限制实现预期结果所需的校正、试验和取样次数,直接获得更高质量的零件,为工具制造商和模具操作员节省时间和金钱。
Setting Expectations with Accurate Simulation
通过精确仿真设定期望
B&J engineers then exported the mold file from Cimatron to Moldex3D injection-molding simulation software for integrated cooling simulation. “The integration between Cimatron and Moldex3D makes it easy to simulate the complete injection-molding cycle, map temperatures across the mold and part to identify hot and cold spots, and simulate the effect of different cooling times,” says Rauch. The simulation also helps highlight areas where redesign may improve the overall cooling strategy before they make any investment in a physical part. Comparative simulations between the original mold design and the new design with conformal cooling lines showed a dramatic improvement in temperature distribution for the new part, reducing temperature variation by 86 percent.
随后,B&J工程师将Cimatron的模具文件导出至Moldex3D注塑成型模拟软件,以进行集成冷却模拟。Rauch说:“Cimatron与Moldex3D的整合,可以很容易地模拟整个注塑成型周期,绘制模具和零件的温度图,以识别热点和冷点,并模拟不同冷却时间的影响。仿真还有助于在对物理部件进行任何投资之前,突出显示重新设计可以改进整体冷却策略的领域。原始模具设计与采用随形冷却管路的新设计之间的比较仿真表明,新零件的温度分布得到了显著改善,温度变化减少了 86%。
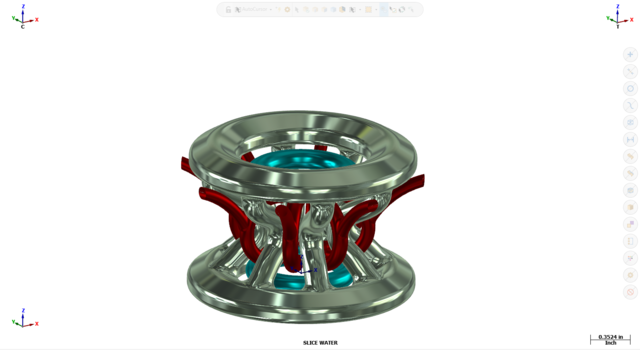
Cimatron与Moldex3D的整合,使得模拟注塑成型周期变得容易,以数字方式评估设计。
3D Printing Mold Inserts with Conformal Cooling Lines
3D打印带随形冷却管路的模具嵌件
B&J engineers then used 3DXpert metal AM software to prepare the mold insert designs for production. They imported the part data, optimized the geometry, calculated the scan-path, arranged the build platform, and sent the job to their in-house ProX DMP 300 metal 3D printer directly from the 3DXpert software.
然后,B&J 工程师使用 3DXpert 金属增材制造软件为生产准备模具镶件设计。他们导入零件数据,优化几何形状,计算扫描路径,安排构建平台,然后直接从 3DXpert 软件将作业发送到其内部的 ProX DMP 300 金属 3D 打印机。
The ProX DMP 300 directs a high-precision laser to build up metal powder particles selectively in thin, horizontal layers, one after the other using LaserForm material. For this automotive duct mold, B&J Specialty used maraging steel material. “The ProX DMP 300 is ideal for producing conformal cooling lines because of its extraordinary accuracy,” Rauch said. “We can hold tolerances of three- or four-thousandths of an inch.” The Cimatron patented direct metal printing (DMP) technology enables smaller material particles to generate the finest feature detail and thinnest wall thicknesses. A surface finish quality of up to 5 Ra μm (200 Ra micro-inches) is achievable and requires less post-processing.
ProX DMP 300 使用 LaserForm 材料引导高精度激光选择性地将金属粉末颗粒堆积在薄的水平层中。对于这种汽车管道模具,B&J Specialty使用了马氏体时效钢材料。“ProX DMP 300 具有非凡的精度,是生产随形冷却管路的理想选择,”Rauch 说。“我们可以保持千分之三或千分之四英寸的公差。”Cimatron 获得专利的直接金属打印 (DMP) 技术使较小的材料颗粒能够产生最精细的特征细节和最薄的壁厚。可实现高达 5 Ra μm(200 Ra 微英寸)的表面光洁度质量,并且需要较少的后处理。
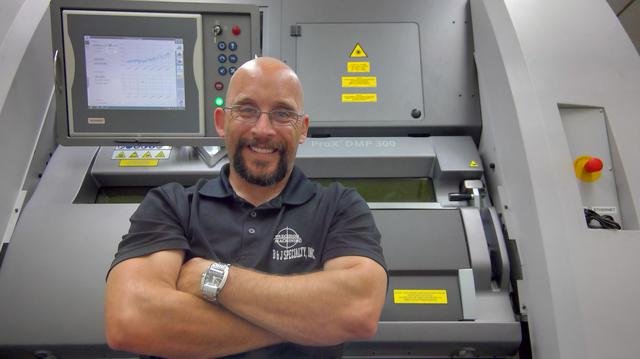
B&J Specialty 使用直接金属 3D 打印提供的随形冷却通道将生产率提高了 30%。
Substantial Gains in Productivity
生产力的大幅提高
After 3D printing, B&J Specialty scanned the inserts into Geomagic Control X inspection and metrology software using a blue laser line 3D scanner and overlaid the mesh on the as-designed geometry to validate the metal 3D-printed mold inserts. The inserts were shipped to the automotive supplier who installed them on its molding machine. “Benchmark testing demonstrated that the more even cooling provided by the conformal lines made it possible to reduce the cycle time and increase productivity throughput by 30 percent,” Rauch said. “We also expect the life of the mold to be substantially higher since the cycle time reductions provided by conformal cooling make it possible to reduce the injection pressure, which in turn reduces wear on the parting line and intricate details of the mold.”
3D打印后,B&J Specialty使用蓝色激光线3D扫描仪将嵌件扫描到Geomagic Control X检测和计量软件中,并将网格覆盖在设计的几何形状上,以验证金属3D打印的模具嵌件。这些嵌件被运送到汽车供应商处,后者将其安装在其成型机上。Rauch 说:“基准测试表明,随形生产线提供的更均匀的冷却可以缩短循环时间并将生产率提高 30%。“我们还预计模具的寿命会大大延长,因为随形冷却可以缩短循环时间,从而降低注射压力,从而减少分型线的磨损和模具的复杂细节。”